HEPA (High-Efficiency Particulate Air) filter terminal boxes are the workhorses of cleanroom air purification. Improper installation can compromise the effectiveness of these vital components, potentially jeopardizing the entire cleanroom's air quality.
Here, we explore key considerations and best practices for a successful HEPA box installation process.
Pre-Installation Planning and Preparation
- Matching Performance to Needs: The foundation of a successful installation lies in selecting a HEPA filter terminal box that aligns perfectly with the cleanroom's design requirements and the specific needs of the customer. Like cleanroom classification (e.g., Class 100, Class 10,000) and desired airflow patterns must be considered during the selection process.
- Meticulous Cleanliness: Maintaining a pristine environment is paramount in cleanrooms. Before installation, a thorough cleaning and sterilization regime is crucial. This includes meticulously cleaning the HEPA box itself (housing, frame, and grill) to remove any dust or debris. Furthermore, the cleanroom environment itself, including the ceiling and air conditioning system, needs rigorous cleaning and filtration (trial operation exceeding 12 hours) to minimize potential contamination during installation.
- Safe Transport and Handling: HEPA filter terminal boxes are delicate instruments. Following the manufacturer's specific transportation guidelines is essential to prevent vibration, collision, or damage during transport to the cleanroom facility.
- Pre-Installation Inspection: Upon arrival at the cleanroom site, the HEPA filter terminal box should undergo a rigorous inspection. This includes verifying the integrity of the filter media, sealant, and frame for any signs of damage. Additionally, confirm that the HEPA box dimensions comply with cleanroom design specifications, and ensure that the product certificate and technical performance data align with the project's requirements.
- Balancing Resistance for Laminar Flow: In cleanrooms requiring laminar airflow (unidirectional airflow with minimal turbulence), ensuring balanced resistance across all HEPA filters within a single HEPA box is critical. The difference between the nominal resistance (expected pressure drop) and the average resistance of each filter station should be less than 5%. This meticulous balancing is crucial for achieving optimal laminar airflow conditions.
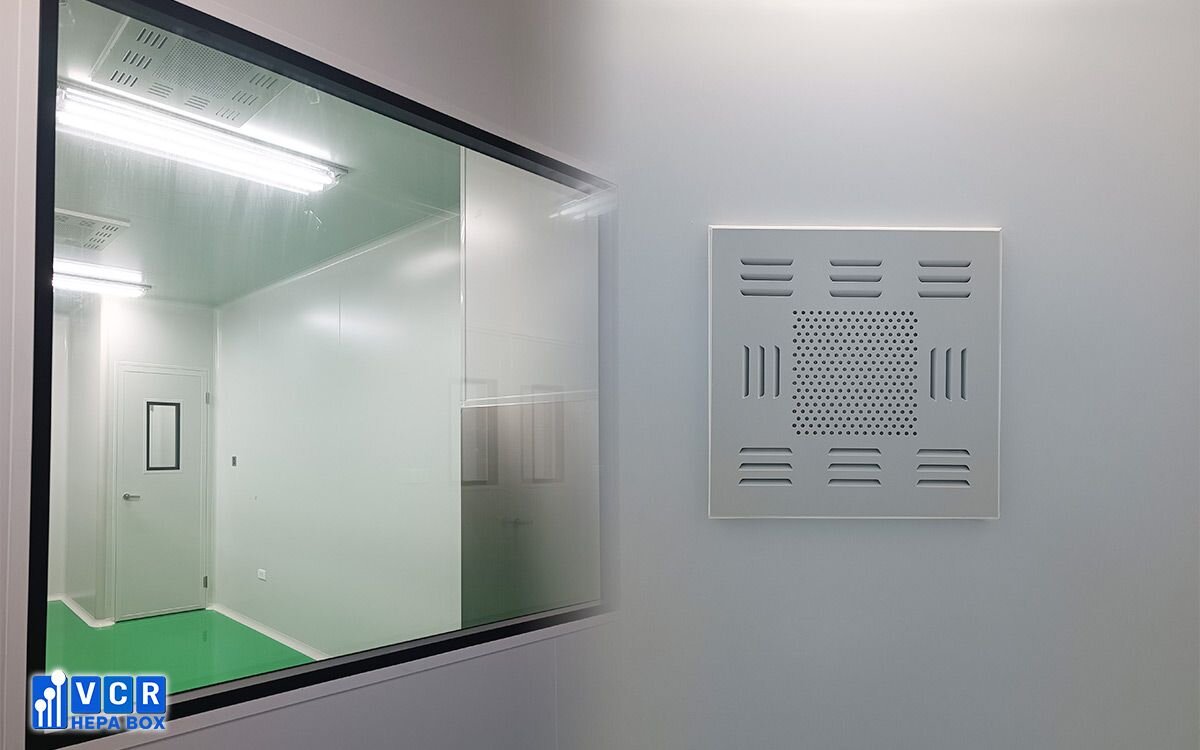
See more: HEPA Box Enclosures for Gel-Seal Filters in Pharmaceutical Cleanrooms
Post-Installation Considerations
- Maintaining Airtightness: A cleanroom's air quality hinges on maintaining a perfect seal. Following installation, ensure a proper gasketed connection between the HEPA box flange and the ceiling plate.
- Preventing Damage: Inspect the HEPA box and its coating for any damage that might have occurred during the installation process. Address any such issues promptly to maintain optimal performance.
- Air Duct Connection: The HEPA box must be securely connected to the cleanroom's air duct system. Seal the open ends of the ducts using plastic film and tape to prevent air leaks.
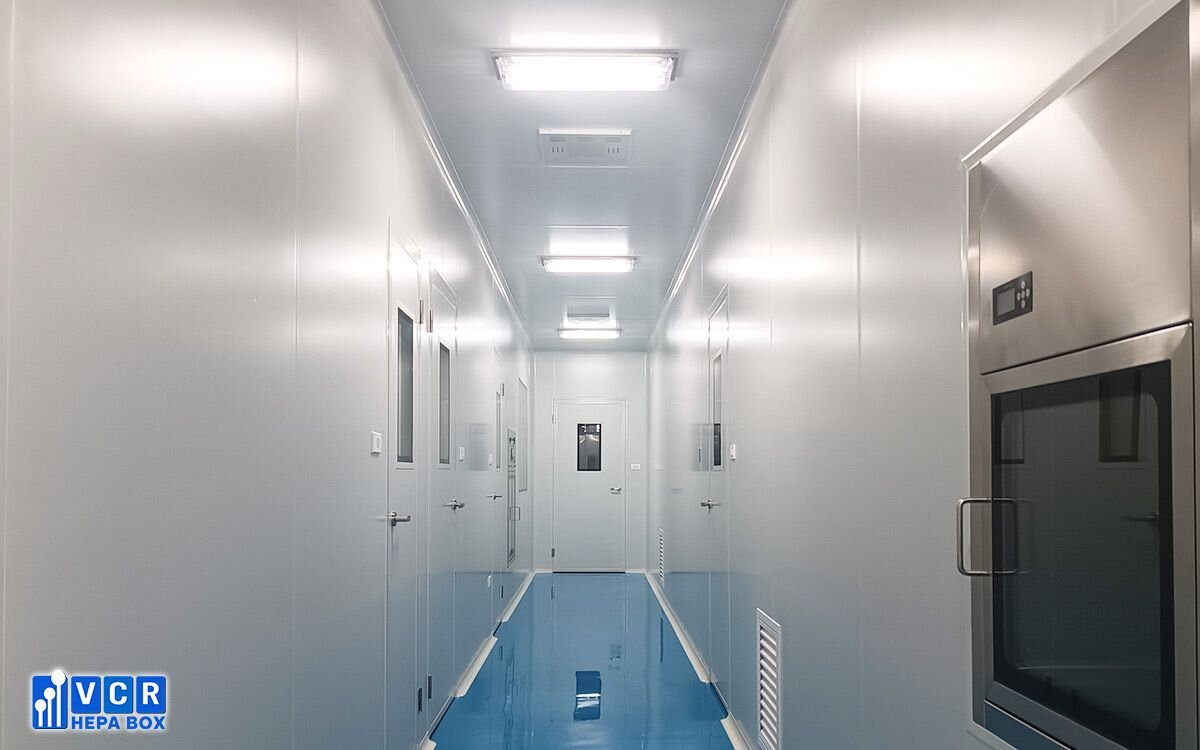
See more: Unveiling the HEPA Box: Guardian of Clean Air in Critical Environments
Conclusion
By adhering to these best practices, facility engineers and cleanroom professionals can ensure a smooth and successful HEPA filter terminal box installation. This meticulous approach safeguards the integrity of the cleanroom environment and paves the way for optimal air quality, a critical factor for various sensitive applications.